Inner Fender Installation:
This week, I installed the aluminum inner fenders into the engine bay. This requires riviting and affixing brackets to the frame. I started with the passenger side. This installation was a BREEZE. As you will see in the pictures, there is a tight fit with the headers but just enough room where I am not worried about any rubbing. Great engineering on Hurricane's part. The driver side was a different matter. The spot that you have to manipulate this large piece of aluminum is very crowed with items like the master cylinders, steering shaft, remote oil lines, etc. I had to use some "persuasion" to get the panel finally in place. Some damage to the fender in the form of scratches, dents and bends occured. I mostly fixed these issues with the magic of scotch brite pads, my rubber mallet and a block of wood. The scotch brite was to remove scratches and give me that cool brushed look. The rubber mallet and wood allowed me to reshape and remove dents in the metal. All the visual spots are untouched. The other parts will be hidden by the body later but the work actually came out OK. I had to reroute on of the remote oil filter lines as you will see in the picture. I am going to create a hose crade out of some wire for this hose so it does not rub on the steering shaft. As you will see in the pictures, the tolerances are very tight on the driver's side. Check out how close the steering shaft next to the panel. It has just enough room to rotate. Fun stuff. Click pictures for a larger image. Enjoy!
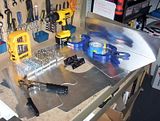
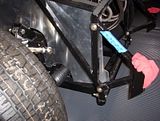
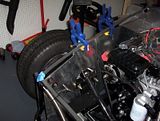
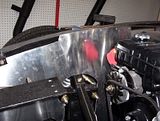
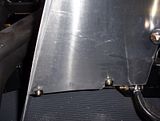
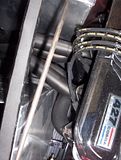
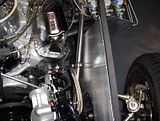
This week, I installed the aluminum inner fenders into the engine bay. This requires riviting and affixing brackets to the frame. I started with the passenger side. This installation was a BREEZE. As you will see in the pictures, there is a tight fit with the headers but just enough room where I am not worried about any rubbing. Great engineering on Hurricane's part. The driver side was a different matter. The spot that you have to manipulate this large piece of aluminum is very crowed with items like the master cylinders, steering shaft, remote oil lines, etc. I had to use some "persuasion" to get the panel finally in place. Some damage to the fender in the form of scratches, dents and bends occured. I mostly fixed these issues with the magic of scotch brite pads, my rubber mallet and a block of wood. The scotch brite was to remove scratches and give me that cool brushed look. The rubber mallet and wood allowed me to reshape and remove dents in the metal. All the visual spots are untouched. The other parts will be hidden by the body later but the work actually came out OK. I had to reroute on of the remote oil filter lines as you will see in the picture. I am going to create a hose crade out of some wire for this hose so it does not rub on the steering shaft. As you will see in the pictures, the tolerances are very tight on the driver's side. Check out how close the steering shaft next to the panel. It has just enough room to rotate. Fun stuff. Click pictures for a larger image. Enjoy!
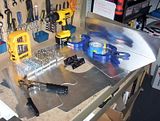
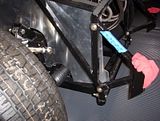
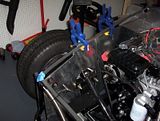
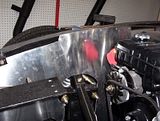
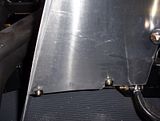
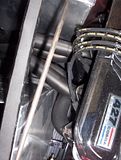
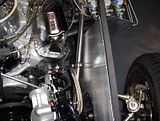
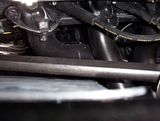